Metal–Organic Frameworks: From Laboratory Marvels to Industrial Game-Changers
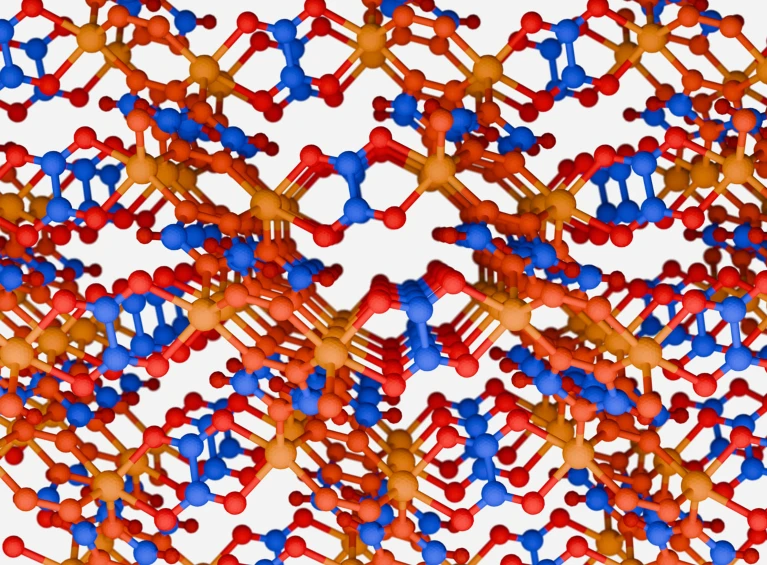
In July 2025, Nature highlighted a major milestone for metal–organic frameworks (MOFs): these highly porous materials, celebrated in academia for over three decades, are finally making their mark in commercial applications. From capturing carbon dioxide at industrial scales to harvesting water in deserts, MOFs are transitioning from lab curiosities to essential tools in addressing global challenges.
The Rise of MOFs: A Brief History
MOFs were first conceptualized in 1989 by chemists Richard Robson and Bernard Hoskins at the University of Melbourne. These materials consist of metallic ions linked by organic molecules, forming molecular scaffolds with vast internal surface areas — sometimes as large as a football field in a single gram of powder. Omar Yaghi later popularized the term "MOF" in the mid-1990s and pioneered methods to make them more robust and versatile.
Over the years, chemists have explored over 100,000 different MOFs in laboratories, investigating their ability to store gases, act as catalysts, and even deliver drugs. However, despite their promise, commercializing these materials proved elusive due to cost and scalability issues.
From Promise to Reality: Carbon Capture and Beyond
The breakthrough came with carbon capture. In Burnaby, Canada, a $150-million factory operated by Svante Technologies now uses MOFs, including the zinc-based CALF-20, to trap CO2 from industrial exhaust gases. This facility represents the first instance of MOFs being produced on an industrial scale.
Other startups, like Nuada in the UK and Promethean Particles, are following suit, aiming to leverage MOFs for carbon capture and storage. Analysts project the MOF market could grow 30-fold by 2035, reaching $930 million.
Besides carbon capture, MOFs are also finding niches in water harvesting and gas filtration. In Death Valley, California, researchers demonstrated a MOF-based device capable of extracting water from arid air. Meanwhile, firms like Numat are developing MOFs for safely storing toxic gases used in semiconductor manufacturing.
Challenges and Future Prospects
The road to widespread adoption is not without hurdles. Manufacturing costs remain high, and the scalability of certain MOFs for industrial purposes is still being tested. Efforts like Wendy Queen’s pilot plant at EPFL Lausanne aim to bridge the gap between lab-scale synthesis and industrial engineering.
Artificial intelligence (AI) is also entering the MOF field. In April 2025, Yaghi’s team demonstrated AI-assisted design of new MOF structures, dramatically reducing the time required to discover promising materials. This convergence of AI and materials science might unlock entirely new applications.
Conclusion
From theoretical marvels to commercial solutions, MOFs exemplify how cutting-edge materials can eventually transform industries and tackle critical environmental challenges. As costs decrease and scalability improves, expect MOFs to play an even larger role in sectors like energy, water, and environmental remediation.
To read the full original article in Nature, visit: https://www.nature.com/articles/d41586-025-02067-y
Sponsored by PWmat (Lonxun Quantum) – a leading developer of GPU-accelerated materials simulation software for cutting-edge quantum, energy, and semiconductor research. Learn more about our solutions at: https://www.pwmat.com/en
📘 Download our latest company brochure to explore our software features, capabilities, and success stories: PWmat PDF Brochure
📞 Phone: +86 400-618-6006
📧 Email: support@pwmat.com
#MetalOrganicFrameworks #CarbonCapture #MaterialsScience #QuantumServerNetworks #MOFs #AdvancedMaterials #EnergyInnovation #PWmat
Comments
Post a Comment